Gunsmith Forge
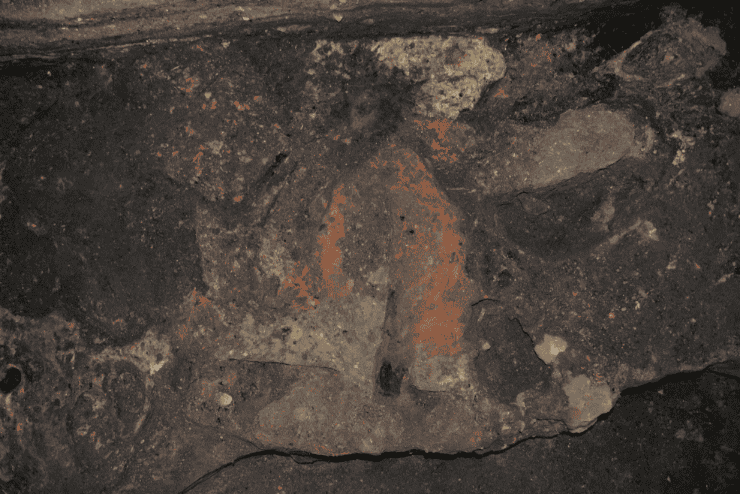
Gun Barrel Manufacturing and Excavation Results
Musket barrels used low-carbon (soft) iron, hammer-forged for strength.First, a plate of iron matching the barrel length was heated in a furnace and wrapped around a cylindrical iron core. The resulting tube was hammered until the joint was no longer visible, in a process called ara-maki, or rough rolling. The barrel was then polished with a file, and sighting and other devices were fitted. The result was a low-quality udon-bari or rough rolling barrel.
For a sturdier barrel, a long, thin steel plate was wound in a spiral around the outside of the barrel and further hammer-forged. This process was called kazura-maki, or vine rolling.
The barrel was then fixed in a hole through a thick wooden post, and the inside of the barrel was finished with a reamer. A removeable breech screw was then plugged into the rear end of the barrel. This screw was essential not only to confine the explosive force of the gunpowder in the barrel, but for removal for barrel cleaning and inspection.
The barrel was trimmed and filed, and then formed, usually into an octagon. The flash pan and gunsights were then attached, and the musket was complete.
Excavations carried out from 2020 to 2022 confirmed the presence of 11 gunsmith's forges in the Old Gunsmith Workshop and Residence. In addition, there were air pipes connecting the furnaces with the bellows, metal and fuel residues melted out during the forging process, and spiral-shaped pieces of iron thought to be parts of kazura-maki barrels.